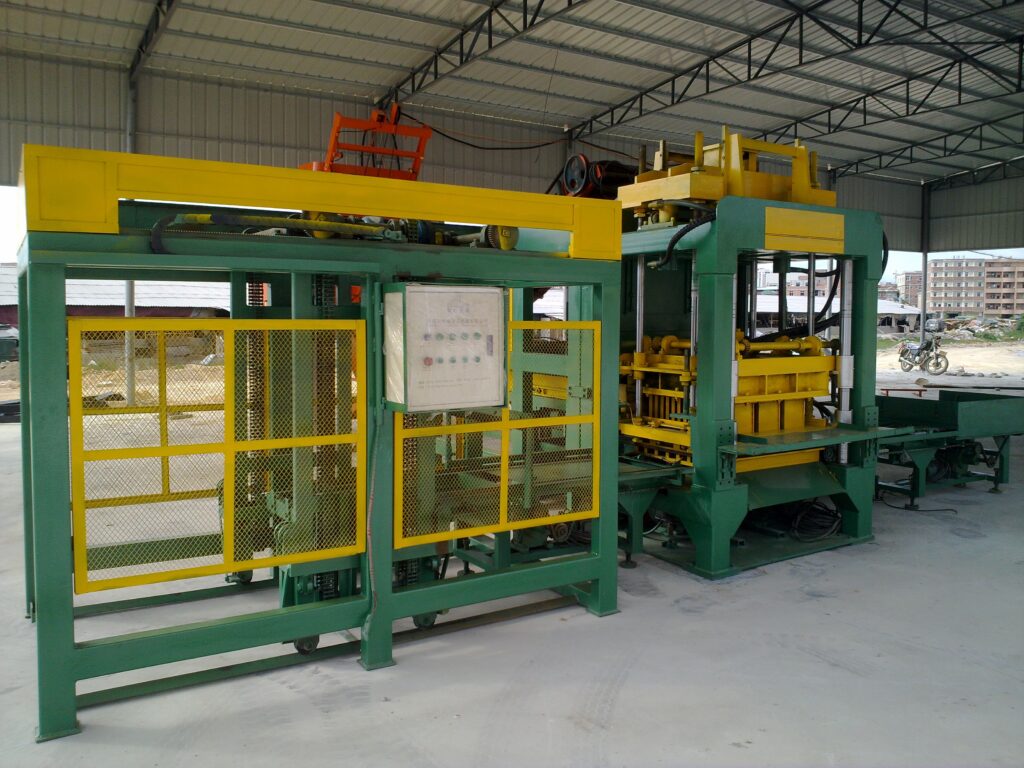
Blocks are essential components in construction, and their quality significantly impacts the durability and strength of structures. Several factors affect the quality of blocks produced, which we’ll explore in detail.
Raw Materials of Blocks
The quality of raw materials is crucial for producing high-quality blocks. Blocks typically consist of cement, aggregates, and water. Each component must meet specific standards:
- Cement: High-quality cement ensures better bonding with aggregates. It should be free from lumps and stored properly1.
- Aggregates: These make up a large portion of a block’s volume. The balance between fine and coarse aggregates affects the water demand and strength of the blocks1.
- Water: Clean water with minimal impurities is essential for proper hydration and curing1.
Mix Design
The proportions of materials in the mix significantly influence block quality. A proper mix design ensures:
- Optimal water-cement ratio: This ratio is crucial for block strength. A lower ratio generally results in stronger blocks but requires precise control1.
- Consistent texture: Proper mixing ensures uniform distribution of materials, directly affecting block quality1.
Block Making Machine
The type and quality of the block making machine play a vital role in producing high-quality blocks. Key features include:
- Material handling system: Ensures accurate feeding of raw materials into the machine.
- Molding system: Determines the uniformity and shape of blocks.
- Compression mechanism: High compression ensures dense and strong blocks.
Production Process of Block Quality
The production process itself affects block quality:
- Mixing: Thorough mixing ensures uniform distribution of materials.
- Molding: Proper molding techniques create blocks with consistent shape and size.
- Curing: Adequate curing is crucial for achieving desired strength. Blocks must be kept in a controlled environment with proper moisture and temperature1.
Quality Control of Blocks
Implementing strict quality control measures throughout the production process is essential:
- Material testing: Regular testing of raw materials ensures consistency.
- Process monitoring: Continuous monitoring during production helps maintain block quality.
- Finished product testing: Testing finished blocks for strength and dimensional accuracy is crucial.
Environmental Factors
Environmental conditions during production and curing can affect block quality:
- Temperature: High temperatures can accelerate curing but may lead to cracks if not controlled properly1.
- Humidity: Proper humidity levels are essential for optimal curing.
Workmanship
The skill and attention to detail of the workers involved in block production significantly impact quality:
- Training: Well-trained workers are more likely to produce high-quality blocks.
- Supervision: Proper supervision ensures adherence to quality standards throughout the production process1.
Standards and Regulations
Adherence to industry standards and local regulations is crucial for producing high-quality blocks:
- Dimensional tolerances: Blocks must meet specified size requirements.
- Strength requirements: Blocks should meet minimum compressive strength standards6.
Storage and Handling of Blocks
Proper storage and handling of finished blocks are important to maintain their quality:
- Protection from elements: Blocks should be stored in a dry place to prevent moisture damage.
- Careful handling: Proper handling techniques prevent damage to blocks during transportation and storage.
Conclusion
In conclusion, producing high-quality blocks requires attention to multiple factors, from raw material selection to the final handling of the product. By optimizing these factors, manufacturers can ensure their blocks meet the highest standards of quality and durability.