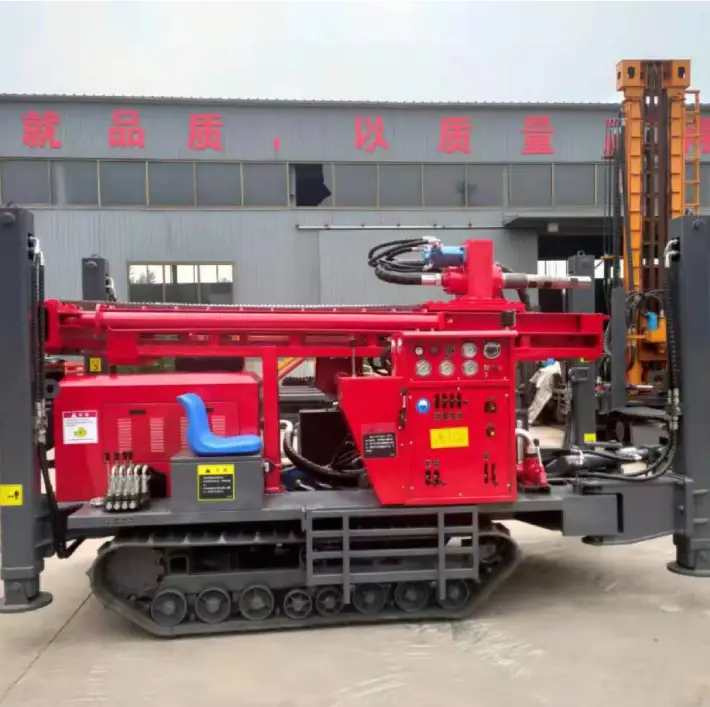
A well drilling machine is essential for accessing underground water resources, especially in areas with limited surface water. These machines use advanced technology and mechanical power to drill deep into the Earth’s surface, creating boreholes for water extraction. Understanding how these machines work and their main components is crucial for efficient operation.
How a Well Drilling Machine Works
A well drilling machine operates by employing either rotary or percussive methods to penetrate the ground.
- Rotary Drilling: This method uses a rotating drill bit to cut through softer geological formations. A rotating mechanism drives the drill bit, which continuously penetrates the earth while flushing out debris using a circulation system.
- Down-the-Hole (DTH) Hammer: This technique is ideal for hard rock formations. It uses pneumatic percussion to break rocks while the drill bit rotates to deepen the borehole.
The drilling process involves:
- Stabilizing the machine at the site using outriggers and leveling jacks.
- Positioning the mast or derrick vertically.
- Operating the drill bit with power transmitted from the machine’s engine.
- Using mud or air to cool the drill bit and remove cuttings from the borehole.
Main Components of a Well Drilling Machine
A well drilling machine consists of several vital components that work together seamlessly:
1. Drilling Rig Host
- The core part of the machine, housing critical components like:
- Drill Pipe: Transmits rotational force.
- Drill Bit: Cuts through soil and rock.
- Drill String: Connects the drill pipe and bit.
2. Power System
- Provides energy for drilling operations, typically through:
- Diesel engines or electric motors.
- Hydraulic systems for smooth operation.
- Air compressors for pneumatic tools like DTH hammers.
3. Transmission System
- Transfers power from the engine to rotate and press down the drill bit. It includes gears, shafts, and hydraulic pumps.
4. Cooling System
- Prevents overheating by circulating fluids to cool the drill bit and other components during operation.
5. Mud Circulation System
- Prepares and circulates drilling fluid (mud) to:
- Cool the drill bit.
- Carry cuttings out of the borehole.
- Stabilize borehole walls.
6. Lifting System
- Includes winches, wire ropes, and pulleys to raise or lower the drill pipe during operations.
7. Guidance System
- Controls the direction of drilling to ensure accuracy in depth and linearity.
8. Control System
- Monitors and adjusts key parameters like speed, pressure, and rotation to ensure safe operations.
Types of Drilling Methods
The choice of drilling method depends on geological conditions.
- Rotary Drilling: Suitable for soft formations; provides continuous penetration.
- DTH Hammer: Effective in hard rock; ensures faster penetration in challenging conditions.
Applications of Well Drilling Machines
Well drilling machines are widely used in:
- Agriculture: For irrigation wells.
- Drinking Water Supply: To access clean groundwater.
- Geological Exploration: For studying subsurface formations.
Conclusion
A well drilling machine is an indispensable tool in groundwater extraction, combining advanced engineering with precision technology. Its main components—such as the drilling rig host, power system, and mud circulation system—work together to ensure efficient and safe operations. By understanding its functions and components, operators can maximize its performance across various applications.